How Alloys in Tool Steel Affect Performance
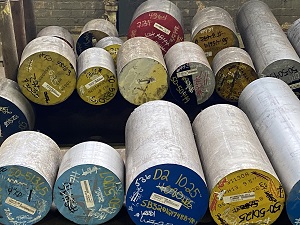
Each individual element in a tool steel imparts certain and specific properties to the steel according to the percentage. The effects of a single alloying element can be modified by the presence of other elements. Below is a chart showing the alloying elements in Cold Work Tool Steels. Read on to learn the effects of each alloying element.
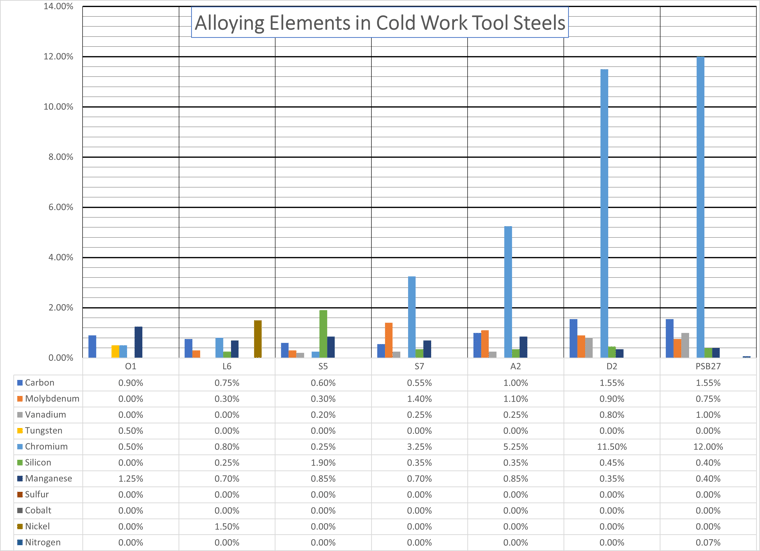
Carbon - C - This is the most important alloying element in steel. With increasing carbon content, the strength and hardenability of the steel increase, but its ductility, formability, weldability, and machinability can be decreased.
Manganese - Mn - Manganese is used as a deoxidizer. It contributes to strength and hardness, but to a lesser extent than carbon. Manganese has a strong effect on increasing the hardenability of steel by reducing the critical cooling rate.
Silicon - Si - Silicon is used as one of the main deoxidizers in steelmaking. Silicon is also absorbed in the melt during steelmaking from furnace and ladle refractory brick. Silicon is a strong promoter of hardenability, improved forgeability and increases scale resistance.
Sulfur - S - For most steels a maximum sulfur limit is specified. Sulfur is intentionally added to certain steels to improve machinability. Sulfur decreases weldability and, in most steels, increases impact toughness and ductility. In Particle Metallurgy steels, however, a controlled sulfur level does improve machinability with negligible effects on other properties.
Nickel - Ni - Nickel increases strength and hardness without sacrificing ductility and toughness.
Aluminum - Al - This is the most effective and frequently used deoxidizer in steelmaking. Small additions are used to insure small grain size. Aluminum will form with nitrogen and form hard aluminum nitrides, which is why it is added to nitriding steels.
Carbon Forming Elements
Chromium - Cr - Chromium is generally added to steel to increase resistance to corrosion and oxidation, to increase hardenability, and to improve high temperature strength. Chromium is a carbide former, which increases edge retention and wear resistance.
Molybdenum - Mo - Molybdenum is usually alloyed together with other elements and is a pronounced carbide former. Molybdenum promotes fine grain structure and improves secondary hardening during tempering. Molybdenum increases strength, hardness and overall toughness.
Tungsten - W - Tungsten is a very pronounced carbide former. It improves toughness and prevents grain growth. Tungsten increases high temperature strength and red hardness. It is primarily used in high speed steels and hot work tool steels.
Vanadium - V - Vanadium is a pronounced carbide former, which increases wear resistance. Vanadium increases strength, hardness and retards grain growth. Vanadium enhances red hardness properties for high speed steels and intensifies the effects of other alloying elements.